Пластик каплау - электроника тармагында, оборона тикшеренүләрендә, көнкүреш техникасында һәм көндәлек кирәк-яракларда киң кулланылган каплау процессы.Пластик каплау процессын куллану күп күләмдә металл материалны саклап калды, эшкәртү процессы гадирәк һәм үз авырлыгы металл материаллар белән чагыштырганда җиңелрәк, шуңа күрә пластик каплау процессын кулланып җитештерелгән җиһазларның авырлыгы кими, шулай ук югары механик көче, матуррак һәм чыдамлы пластик өлешләрнең күренеше.
Пластик каплауның сыйфаты бик мөһим.Пластик каплау сыйфатына йогынты ясаучы күп факторлар бар, шул исәптән каплау процессы, эксплуатация һәм пластик процесс, алар пластик каплау сыйфатына зур йогынты ясый ала.
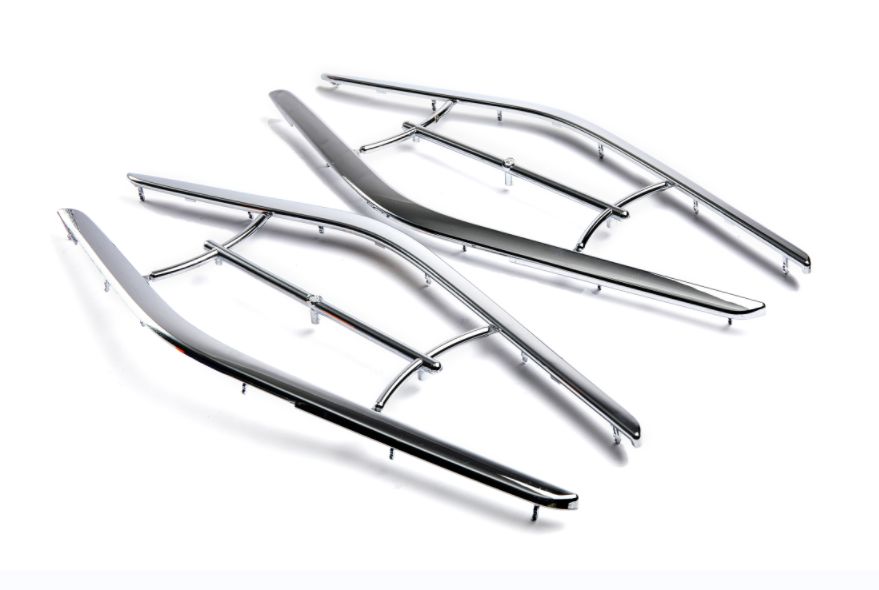
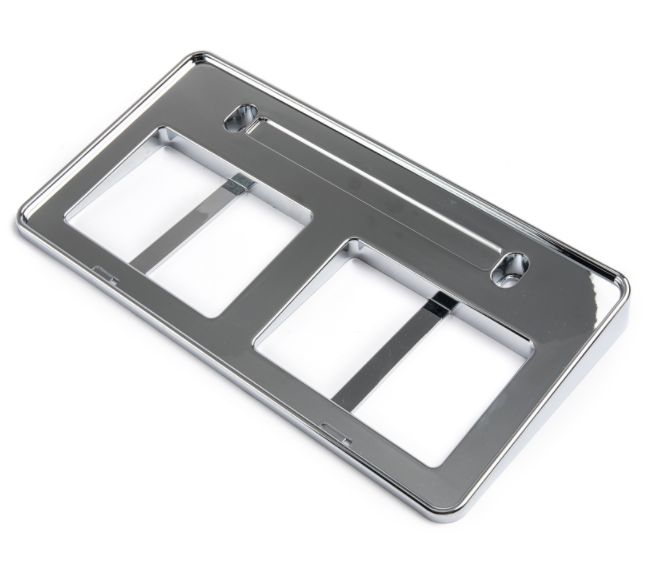
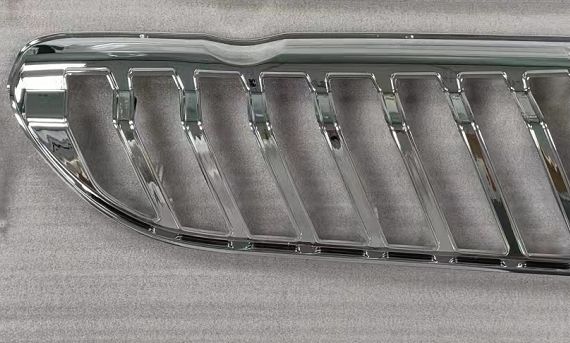
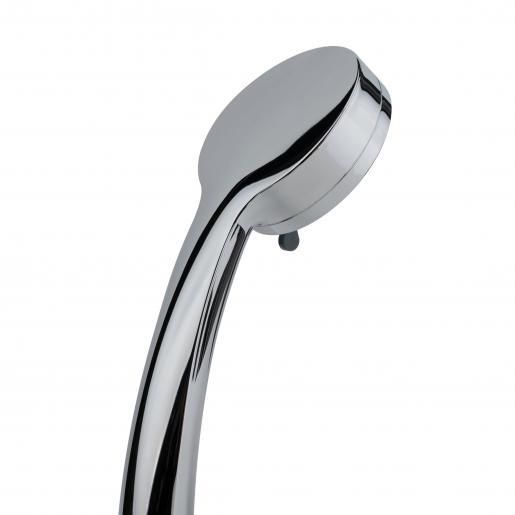
1. Чимал сайлау
Базарда пластмассаның төрле төрләре бар, ләкин барысын да каплап булмый, чөнки һәр пластикның үз үзенчәлекләре бар, һәм пластинка белән пластмасса белән металл катлам арасындагы бәйләнешне һәм физик үзлекләр охшашлыгын исәпкә алырга кирәк. пластик һәм металл каплау.Хәзерге вакытта пластмасса өчен ABS һәм PP.
2. Детальләр формасы
А).Пластик өлешнең калынлыгы бертөрле булырга тиеш, пластик өлешнең кысылуына китергән тигезсезлектән, каплау тәмамлангач, аның металл яктылыгы бер үк вакытта кыскаруга китерә.
Theәм пластик өлешнең стенасы артык нечкә булырга тиеш түгел, югыйсә ул каплау вакытында җиңел деформацияләнәчәк һәм каплау бәйләнеше начар булыр, ә катгыйлыгы кимер һәм куллану вакытында каплау җиңел төшеп калыр.
Б).Сукыр тишекләрдән сакланыгыз, югыйсә сукыр соленоидтагы калдык эшкәртү эремәсе җиңел чистартылмас һәм киләсе процесста пычрануга китерер, шулай итеп каплау сыйфатына тәэсир итәр.
В).Әгәр дә каплау үткен кырлы булса, каплау катлаулырак булачак, чөнки үткен кырлар электр җитештерүгә китереп кенә калмый, шулай ук почмакларда каплауның көчәюенә китерәчәк, шуңа күрә сез радиус белән түгәрәк почмак күчүен сайларга тырышырга тиеш. ким дигәндә 0,3 мм.
Тигез пластик өлешләрне каплаганда, самолетны бераз түгәрәк формага үзгәртергә яки каплау өчен мат өслеген ясарга тырышыгыз, чөнки яссы форма нечкә үзәк белән тигез булмаган каплагычка һәм калын кыр белән капланган вакытта булачак.Шулай ук, каплау ялтыравыкларының бердәмлеген арттыру өчен, бераз параболик формага ия булу өчен, пластмасса өлешләрен зур каплау өслеге мәйданы белән эшләргә тырышыгыз.
Г).Пластик өлешләрдәге каникулларны һәм чыгу урыннарын киметегез, чөнки тирән чокырлар пластмассаны каплаганда пластмассаны ачалар, чыгу урыннары яна.Чокырның тирәнлеге трюк киңлегенең 1/3 өлешеннән артмаска тиеш, аскы түгәрәкләнергә тиеш.Гриль булганда, тишекнең киңлеге нур киңлегенә тигез булырга һәм калынлыкның 1/2 өлешеннән ким булырга тиеш.
Д).Monthитәрлек монтаж позицияләре капланган өлештә эшләнергә тиеш, асылынган корал белән контакт өслеге металл өлешенә караганда 2-3 тапкыр зуррак булырга тиеш.
Ф).Пластик өлешләр формада капланырга һәм капланганнан соң демоулировать ителергә тиеш, шуңа күрә конструкция пластик өлешләрнең җиңел җиңел булуын тәэмин итәргә тиеш, шуңа күрә капланган өлешләр өслеген эшкәртмәскә яки пластинка бәйләнешенә тәэсир итмәскә. .
G).Пычрак кирәк булганда, селкенү юнәлеше демулинг юнәлеше белән һәм туры сызыкта булырга тиеш.Пычрак полосалар белән полосалар арасы мөмкин кадәр зур булырга тиеш.
Н).Пластик өлешләр кертүне таләп итә, каплау алдыннан эшкәртүнең коррозицион характеры аркасында мөмкин кадәр металл кертүдән сакланыгыз.
I).Әгәр дә пластик өлешнең өслеге бик шома булса, бу каплау катламы формалаштыру өчен уңайлы түгел, шуңа күрә икенчел пластик өлешнең өслеге билгеле өслек тупаслыгы булырга тиеш.
3. Дизайн һәм җитештерү
А).Форма материалы бериллий бронза эретмәсе түгел, ә югары сыйфатлы вакуум чуен корычтан ясалырга тиеш.Бушлыкның өслеге тигезлектә 0,21 ммнан ким булмаган форма яктылыгы көзгесен яктырту өчен бизәлгән булырга тиеш, һәм өслеге каты хром белән капланган булырга тиеш.
Б).Пластик өлешнең өслеге форма куышлыгының өслеген чагылдыра, шуңа күрә электроплатланган пластик өлешнең форма куышлыгы бик чиста булырга тиеш, һәм форма куышлыгының өслеге тупаслыгы өслек өслегенең тупаслыгыннан 12 класска югарырак булырга тиеш. өлеше.
В).Аеру өслеге, кушылу сызыгы һәм үзәк кертү сызыгы капланган өслектә эшләнергә тиеш түгел.
Г).Капка өлешнең иң калын өлешендә эшләнергә тиеш.Бушлыкны тутырганда эретү бик тиз суынмасын өчен, капка мөмкин кадәр зур булырга тиеш (гадәти инъекция формасыннан якынча 10% зуррак), яхшырак капка һәм чишмәнең түгәрәк киселеше һәм озынлыгы. чишмә кыскарак булырга тиеш.
Д).Airава филаментлары һәм өлеш өслегендә күбекләр кебек кимчелекләрдән саклану өчен, газ тишекләре бирелергә тиеш.
Ф).Эйектор механизмы өлешнең формадан шома чыгарылышын тәэмин итәрлек итеп сайланырга тиеш.
4. Пластик өлешләр өчен инъекция формалаштыру процессы шартлары
Инъекция формалаштыру процессының характеристикалары аркасында эчке стресслар котылгысыз, ләкин процесс шартларын дөрес контрольдә тоту эчке стрессларны минимумга кадәр киметәчәк һәм өлешләрнең нормаль кулланылышын тәэмин итәчәк.
Түбәндәге факторлар процесс шартларының эчке стрессына тәэсир итә.
А).Чимал киптерү
Инъекция формалаштыру процессында, каплау өчен кулланылган чимал җитәрлек коры булмаса, өлешләр өслеге җиңел һава филаментлары һәм күбекләр чыгарачак, бу каплау күренешенә һәм бәйләү көченә тәэсир итәчәк.
Б).Көле температурасы
Форманың температурасы каплау катламының бәйләү көченә турыдан-туры тәэсир итә.Форманың температурасы югары булганда, резин яхшы агып китәчәк һәм өлешнең калдык стрессы кечкенә булачак, бу каплау катламының бәйләү көчен яхшырту өчен ярдәм итә.Әгәр дә форманың температурасы бик түбән булса, ике каплагычны формалаштыру җиңел, шуңа күрә металл капланганда металл салынмасын.
В).Температураны эшкәртү
Әгәр эшкәртү температурасы артык югары булса, ул тигез булмаган кысылуга китерәчәк, шулай итеп күләм температурасы стрессын арттырачак, һәм мөһер басымы да күтәреләчәк, шома демолдинг өчен суыту вакытын таләп итә.Шуңа күрә эшкәртү температурасы артык түбән дә, артык югары да булырга тиеш түгел.Пластик агып китмәсен өчен, авыз температурасы баррель максималь температурасыннан түбән булырга тиеш.Салкын материалны форма куышлыгына кертмәс өчен, кисәкләр, ташлар һәм башка җитешсезлекләр җитештерүдән саклану һәм начар каплау комбинациясенә китерү.
Г).Инъекция тизлеге, вакыт һәм басым
Әгәр дә бу өчесе яхшы үзләштерелмәсә, ул калдык стрессының артуына китерәчәк, шуңа күрә инъекция тизлеге әкрен булырга тиеш, инъекция вакыты мөмкин кадәр кыска булырга тиеш, һәм инъекция басымы артык югары булырга тиеш түгел, бу калдыкны эффектив киметәчәк. стресс.
Д).Суыту вакыты
Суыту вакыты контрольдә тотылырга тиеш, шуңа күрә форма куышлыгындагы калдык стресс бик түбән дәрәҗәгә төшә яки форма ачылганчы нульгә якын.Әгәр суыту вакыты бик кыска булса, мәҗбүри демулдинг өлештә зур эчке стресска китерәчәк.Ләкин, суыту вакыты артык озын булырга тиеш түгел, югыйсә җитештерү нәтиҗәлелеге түбән генә түгел, суытуның кысылуы өлешнең эчке һәм тышкы катламнары арасында киеренкелек стрессына китерәчәк.Бу икесенең дә пластмасса өлешендәге бәйләнешне киметәчәк.
Ф).Чыгару агентларының йогынтысы
Пластик өлешләр өчен чыгаргыч агентларны кулланмаска яхшырак.Нефть нигезендә чыгаручы агентларга рөхсәт ителми, чөнки алар пластик өлешнең өслек катламына химик үзгәрешләр китерергә һәм аның химик үзлекләрен үзгәртергә мөмкин, нәтиҗәдә каплау начар бәйләнешкә китерә.
Чыгарылыш агенты кулланылырга тиеш булган очракта, форманы чыгару өчен талкум порошогы яки сабынлы су гына кулланылырга тиеш.
Пластинка процессында төрле йогынты ясаучы факторлар аркасында, пластик өлешләр төрле дәрәҗәдәге эчке стресска дучар булалар, бу каплау бәйләнешенең кимүенә китерә һәм каплау бәйләнешен арттыру өчен эффектив дәвалау таләп итә.
Хәзерге вакытта җылылык белән эшкәртү һәм өслекне бизәү агентлары белән эшкәртү пластик өлешләрдәге эчке стрессларны бетерүгә бик яхшы йогынты ясый.
Моннан тыш, капланган өлешләрне тутырырга һәм чиктән тыш игътибар белән тикшерергә кирәк, һәм капланган өлешләрнең тышкы кыяфәтенә зыян китермәс өчен махсус төрү эшләнергә тиеш.
Сямен Руйченг Индустриаль Дизайн Ко., ООО Пластик каплау буенча бай тәҗрибәгә ия, кирәк булса, безгә мөрәҗәгать итегез!
Пост вакыты: 22-2023 февраль